We’re beginning with molecular design and 3D microprinting analysis at the moment, earlier than transferring on to a robotic 3D printer partnership. Then it’s on to a wide range of functions, together with a 3D printed concrete bridge, 3D printed furnishings, 3D printed shoe soles, and at last 3D printed prosthetic sockets.
Researchers Use Molecular Design for Additive 3D Microprinting
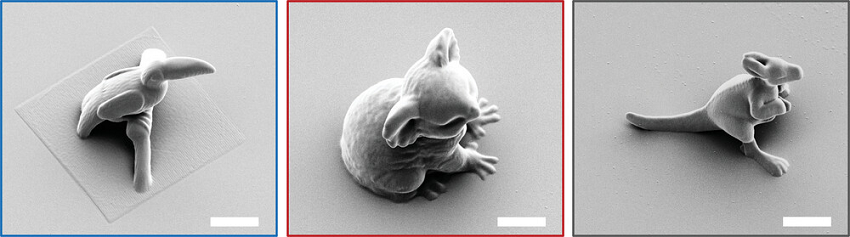
Consultant SEM photos of 3D microstructures printed with 2PLP with alternating (blue), triblock (crimson), and block (grey) oligomer inks printed with 0.25 wt.% DETC demonstrating versatility of the oligomers as inks for 3D microprinting. Scale = 10 µm. (Reprinted with permission from Wiley-VCH Verlag)
You’ll find macromolecules with complicated, outlined constructions in nature, however not usually in artificial macromolecules. Sequence-defined approaches allow extra exact management of the macromolecular construction, however aside from area of interest sectors like knowledge encryption, there aren’t many functions. However, a workforce of researchers from Heidelberg College and the Max Planck Institute for Medical Analysis used rational molecular design to direct sequence-defined supplies as 3D printable inks. By combining two-photon laser printing (2PLP) on the microscale with sequence-defined macromolecules, they may program print decision, mechanics, and fabrication limits to develop exact, intricately structured supplies.
The researchers formulated three inks by synthesizing oligomers, and used them to 3D print very intricate “buckyball” constructions. Utilizing sequence-based management to dictate the print behaviors, the workforce then microprinted intricate vegetation, mammals, and birds. By “manipulating the positioning of photocrosslinkable models alongside an oligomer spine,” they had been in a position to program main variations within the topology, print decision, mechanics, and fabrication home windows of the microscale prints. This skill to make use of sequence design to tailor 3D printable inks has many potential functions for developing specialised units, reminiscent of focused drug supply automobiles, lab-on-a-chip and bio-integrated electronics, labeled cell progress scaffolding, and even molecular circuit elements. You possibly can study extra about their work of their revealed paper.
TGS Providing Flexbot Analysis XL for Czech Republic Prospects
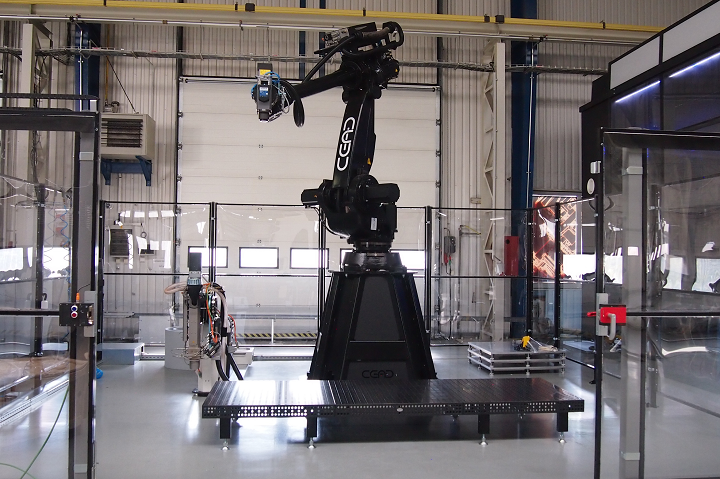
Flexbot Analysis XL platform put in at TGS. Photograph Credit score: TGS
Dutch firm CEAD, a pioneer in robotic giant format additive manufacturing (LFAM) options, introduced a partnership with superior engineering agency TGS, positioned in Mýto, Czech Republic. At an open home in December, TGS launched its new Flexbot Analysis XL platform, which the CEAD workforce had put in in September. Attendees acquired to see dwell demonstrations of the Flexbot Analysis XL, printing with Airtech Superior Supplies Group’s Dahltram T-100GF fiberglass composite that’s strengthened with recycled-grade co-polyester resin. With a print quantity of as much as 3 x 1 x 2.5 meters and a flexible vary of composite supplies—together with PEEK and glass- or fiber-reinforced—the novel large-format printer will enable TGS to supply 3D printing providers to its clients within the Czech Republic. Moreover, TGS can even function a reseller for CEAD’s Flexbot and extruders within the nation and different close by areas.
“The open day occasion highlighted as soon as once more the significance of the strategic partnership between CEAD and TGS. This synergy will leverage our competencies to help clients within the implementation journey for large-format additive manufacturing options in Czeck and Slovakia markets,” mentioned Andrea Baldolini, gross sales workforce lead at CEAD.
Holcim Unveils Round 3D Printed Concrete Bridge
Sustainable constructing options chief Holcim launched a bridge that’s mentioned to be the primary of its form: Phoenix, a round, 3D printed concrete masonry bridge that stands by compression with out reinforcement. The bridge, positioned at Holcim’s Innovation Hub in Europe, was constructed utilizing its proprietary ECOCycle round expertise and a {custom} concrete ink with 10 tons of recycled supplies inside. Holcim partnered with the Block Analysis Group at ETH Zurich, Zaha Hadid Architects Computation and Design Group, and incremental3D to create the bridge, which demonstrates how combining round development and 3D concrete printing can allow low-carbon infrastructure functions. As Holcim defined, “Phoenix resulted from the partial recycling of aggregates” from the unique blocks of 3D concrete printed bridge Striatus, launched by these identical companions throughout the 2021 Venice Biennale of Structure.
“I’m thrilled to unveil Phoenix, a monument to sustainability and the results of a fruitful collaboration with our companions to satisfy a standard aim: demonstrating that important infrastructure might be designed and inbuilt a approach that’s round and lowcarbon at the moment,” said Edelio Bermejo, Head of World R&D, Holcim. “This challenge showcases the affect that innovation can have in Holcim’s mission to decarbonize constructing for a net-zero future.”
OZRUH Launches Furnishings Assortment Made with 3D Printed Sand
London-based architectural design agency OZRUH, based in 2019, creates designs which can be novel and clever and, because it states on the web site, “made by the rules of divergent evolution, superior computational processes, and modern manufacturing strategies.” Its newest furnishings assortment undoubtedly matches—each bit in PRIMITIVES [1] is 3D printed utilizing recyclable quartz sand particles. Every sculptural, detailed nightstand within the assortment exhibits the agency’s exploration of making voxel-based shell geometries by controlling erosion. The strategy used to print the items relies on binder jetting, and the gathering marries modern aesthetics and sustainability. Quartz sand, which might be recycled a number of occasions, is the principle materials, and a dissolvable materials binds the sand with out the usage of excessive temperatures, which improves manufacturing effectivity and helps sustainability.
“The aim is to make designs that blur the distinction between archaeological and geological types to intention for higher longevity than typical modernist geometries. Permitting the items to be extra receptive to adapting to surprising circumstances, exterior pressures, and erosion. This vary of sculptural furnishings demonstrates how we will use 3D printing strategies to push formal experimentation and novelty with new functions of historic supplies to create long-lasting purposeful artwork,” mentioned Levent Ozruh.
“Our studio believes that embracing the concept of antifragility* in architectural design provides an incredible alternative to find new methods to create shapes and constructions whereas additionally making designs extra sustainable. This mind-set is just like how we see pure supplies like rocks as full, even when they’ve some irregularities – differentiating from fashionable design, the place even a small chip on a dice’s nook is seen as harm.”
Made Plus Inc Utilizing ETEC Xtreme 8K for Planet-Constructive Footwear
U.S.-based footwear firm Made Plus Inc. (made+), a Desktop Steel buyer, is pioneering planet-positive manufacturing, and utilizing the ETEC Xtreme 8K DLP 3D printer to make sneakers. Along with 3D printing, the corporate makes use of machine knitting and digital modeling in its on-demand manufacturing mannequin. Prospects can go to the all-in-one product customization platform to select from a whole bunch of shade mixtures for his or her sneakers, which provide a selection of both a traditional polyurethane cushioning system or an unique 3D printed lattice insole. Every pair within the firm’s debut shoe assortment, the Skiff, is made in Maryland, incorporates azo-free dyes, and has a classy, modern design. Observe made+ on Instagram to get 10% off your subsequent {custom} order with the promo code M+instagram.
“Our modern method to creating sneakers not solely ensures high quality, match and efficiency but additionally aligns with a accountable, environmentally acutely aware life-style,” the corporate states on its web site.
“By selecting made+ footwear, you’re making a acutely aware determination that positively impacts our planet with out sacrificing feel and look.”
Snapform & Create it Actual 3D Printing Prosthetic Sockets with FDM
Prosthetic clinic Snapform, based mostly on the Technical College of Denmark (DTU), is devoted to enhancing the lives of amputees by reimagining how one can make inexpensive, custom-fitted prosthetics with the newest digital expertise, together with its prosthetic becoming engine SimFit. Not too long ago, the corporate was excited to share that it’s made constructive progress in exploring the potential of Fused Deposition Modeling (FDM) as a method to make prosthetic sockets. This technique is normally regarded as not robust sufficient for prosthetics, and lots of desire to make use of Selective Laser Sintering (SLS) as an alternative. This work happened by a collaboration with fellow Danish firm Create it REAL to analyze and take a look at the capabilities of FDM printing for prosthetic sockets. Snapform carried out a power take a look at on an FDM printed socket made by Create it REAL, and introduced in a LinkedIn put up that “it handed the utmost power take a look at in keeping with ISO 10328.”
“The potential affect of this achievement is big. With Snapforms Simfit program mixed with Creat It Actual’s printing expertise, there’s a big alternative to dramatically cut back the price of prosthetics. This breakthrough opens doorways for numerous amputees worldwide who at present lack entry to high-quality prosthetics.”
Subscribe to Our E-mail Publication
Keep up-to-date on all the newest information from the 3D printing trade and obtain data and provides from third social gathering distributors.